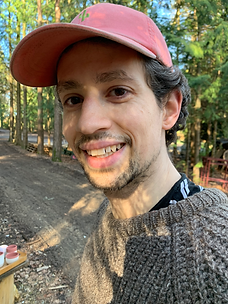
Hello, hi!

My Background

My grandma was a potter, who trained under Joanna Constantinidis, and worked a lot with porcelain. This is her on her wheel,
​
When she passed away, her electric Brent wheel was put away in the shed, where it sat for several years before I realised it was there. I brought it into my parents' dining room, and quickly learnt that most of the tools needed to throw could be found in a kitchen drawer.
​
I taught myself how to throw, and practiced in the Bristol University Student Union pottery studio for 3 years, before joining Petr Weigl Studio in London, where I was surrounded by a group of incredible potters and ceramicists. I learnt a lot there, from watching and talking, and also had some lessons from Ian Thompson which helped me to unpick the bad habits I had developed
​
I now work out of pottery that I established in a community woodland in East Sussex - Wilderness Wood - where I make and fire all my pieces, including supplying the community with functional ware, such as mugs for the coffee shop and bowls for the residents.
​
​
The Wood Firing Process
For the first 6 years of doing pottery, I fired all my work in electric kilns.
​
When I moved to the woods, there was a decision to be made about what kiln we would buy or make, and all signs pointed to building a wood fired one. Wilderness Wood is a working woodland, so not only was there a constant supply of fuel for firings and ash for glazes, but the spirit of the community was one which felt in line with doing things differently and from scratch.
​
Besides, when I mentioned the idea of building a wood kiln to other potters, there was an explosion of excitement and encouragement, pointing me towards a world of glazing and making that I was entirely unaware of.
​
As it turns out, the same glaze put into an electric kiln, will produce a galaxy of depth when fired in a wood kiln. My glazing theory is very weak, but know - from what I've seen - that ash settled in the glaze, and flames scorch the clay. Oxygen ebbs and flows, causing the glazes do totally different things to a regular electric kiln. It's beautiful!
​​
Most potters will tell you how terrifying but exciting it is opening a kiln, and I've found
that this emotional rollercoaster is even better (or worse!) with the wood kiln.​
​

The Fast Fire Kiln
The kiln is built to the design of Fred Olsen's Fast Fire kiln. I retrieved a copy of the Kiln Book from the British Library, and had the expert knowledge of Matthew Bayman to guide me with all of my questions about the build theory.
​
The bricks were also salvaged from a retired salt kiln that Sarah Walton had built and recently dismantled.
​
You can watch a timelapse of the kiln build here.